Understanding the concept of "pick on pull" is essential in various contexts, from manufacturing and logistics to personal productivity. Whether you're looking to streamline your operations or improve your workflow, this guide will walk you through everything you need to know about pick on pull. Discover how this approach can transform your processes and drive efficiency.
In today's fast-paced world, businesses and individuals are constantly seeking ways to optimize their performance. One of the most effective strategies that have emerged is the "pick on pull" methodology. This concept focuses on demand-driven processes, ensuring resources are allocated only when needed. As a result, it minimizes waste and maximizes productivity.
This article delves into the intricacies of pick on pull, offering actionable insights and expert advice. Whether you're new to the concept or looking to refine your understanding, this guide is designed to help you harness the full potential of pick on pull in your operations.
Read also:Unleashing Potential The Ultimate Guide To Sports Academy Logan
Table of Contents
- What is Pick on Pull?
- History of Pick on Pull
- Benefits of Pick on Pull
- Implementing Pick on Pull
- Common Challenges in Pick on Pull
- Tools for Pick on Pull
- Real-World Applications of Pick on Pull
- Pick on Pull vs Other Methods
- Future of Pick on Pull
- Conclusion
What is Pick on Pull?
The term "pick on pull" refers to a demand-driven system where items or tasks are initiated only when there is actual demand. This approach contrasts with traditional push systems, where production or processes are based on forecasts rather than real-time needs. By aligning supply with demand, pick on pull ensures resources are utilized efficiently, reducing waste and improving overall performance.
This methodology is particularly effective in industries such as manufacturing, logistics, and retail. It emphasizes the importance of responsiveness and adaptability, making it an ideal choice for businesses operating in dynamic environments.
Key principles of pick on pull:
- Demand-driven processes
- Reduced inventory levels
- Improved resource allocation
- Enhanced customer satisfaction
How Pick on Pull Works
The implementation of pick on pull involves several critical steps. First, businesses must establish clear demand signals, ensuring that production or tasks are triggered only when necessary. Next, they need to develop a robust system for tracking and managing these signals, leveraging technology and data analytics to optimize performance.
Additionally, training employees to understand and adhere to pick on pull principles is crucial. By fostering a culture of efficiency and responsiveness, organizations can fully realize the benefits of this methodology.
History of Pick on Pull
The origins of pick on pull can be traced back to the Toyota Production System (TPS), which introduced the concept of Just-In-Time (JIT) manufacturing. This revolutionary approach transformed the manufacturing industry by emphasizing waste reduction and efficiency. Over time, the principles of JIT evolved into the pick on pull methodology, which has since been adopted across various sectors.
Read also:Unveiling The Truth Did Judy Collins Have A Stroke
According to research published in the Journal of Operations Management, companies that have implemented pick on pull have experienced significant improvements in productivity and cost efficiency. These findings underscore the importance of understanding the historical context of pick on pull to appreciate its evolution and relevance today.
Key Milestones in Pick on Pull Development
- 1950s: Introduction of JIT by Toyota
- 1980s: Global adoption of JIT principles
- 2000s: Expansion of pick on pull beyond manufacturing
Benefits of Pick on Pull
Adopting a pick on pull strategy offers numerous advantages for businesses and individuals alike. Below are some of the most significant benefits:
1. Reduced Waste
By aligning production with demand, pick on pull eliminates unnecessary inventory and minimizes waste. This is particularly important in industries where perishable goods or limited shelf-life products are involved.
2. Improved Efficiency
Pick on pull streamlines processes, ensuring that resources are allocated only when needed. This leads to faster turnaround times and increased productivity.
3. Enhanced Customer Satisfaction
With pick on pull, businesses can respond more effectively to customer demands, ensuring timely delivery and high-quality service. This, in turn, fosters customer loyalty and drives growth.
Implementing Pick on Pull
Successfully implementing pick on pull requires careful planning and execution. Below are some essential steps to consider:
Step 1: Identify Demand Signals
Establish clear indicators of demand, such as customer orders or inventory levels. These signals will serve as triggers for initiating production or tasks.
Step 2: Develop a Tracking System
Implement a reliable system for monitoring and managing demand signals. This may involve using software solutions or manual processes, depending on the scale of operations.
Step 3: Train Employees
Ensure that all employees understand the principles of pick on pull and their role in its implementation. Provide comprehensive training to foster a culture of efficiency and responsiveness.
Common Challenges in Pick on Pull
While pick on pull offers numerous benefits, it also presents certain challenges. Below are some common obstacles businesses may encounter:
Challenge 1: Resistance to Change
Implementing a new system can be met with resistance from employees accustomed to traditional methods. Addressing this challenge requires effective communication and change management strategies.
Challenge 2: Technological Limitations
Some organizations may lack the necessary technology to support pick on pull operations. Investing in appropriate software and infrastructure is crucial for overcoming this hurdle.
Challenge 3: Forecasting Accuracy
While pick on pull focuses on demand-driven processes, accurate forecasting remains essential for anticipating future needs. Developing reliable forecasting models is key to addressing this challenge.
Tools for Pick on Pull
Various tools and technologies can facilitate the implementation of pick on pull. Below are some of the most effective options:
1. Inventory Management Software
Software solutions such as SAP and Oracle provide robust tools for tracking inventory levels and managing demand signals.
2. Data Analytics Platforms
Platforms like Tableau and Power BI enable businesses to analyze data and identify trends, enhancing their ability to respond to demand effectively.
3. Communication Systems
Effective communication is vital for coordinating pick on pull operations. Tools such as Slack and Microsoft Teams can streamline communication and collaboration within teams.
Real-World Applications of Pick on Pull
Pick on pull has been successfully implemented in various industries, with impressive results. Below are some notable examples:
Example 1: Manufacturing
Toyota, the pioneer of pick on pull, continues to benefit from this methodology. By aligning production with demand, Toyota has achieved significant cost savings and improved efficiency.
Example 2: Retail
Retail giants like Walmart have adopted pick on pull to optimize their supply chain operations. This has enabled them to maintain low inventory levels while ensuring timely delivery of products.
Example 3: Healthcare
In the healthcare sector, pick on pull is used to manage medical supplies and equipment. This ensures that resources are available when needed, improving patient care and reducing costs.
Pick on Pull vs Other Methods
While pick on pull offers numerous advantages, it is important to compare it with other methodologies to determine its suitability for specific contexts. Below is a comparison of pick on pull with traditional push systems:
Push Systems
Push systems rely on forecasts to determine production levels, often resulting in excess inventory and waste. In contrast, pick on pull focuses on demand-driven processes, minimizing these issues.
Pull Systems
Pick on pull is a subset of pull systems, which also emphasize demand-driven operations. However, pick on pull specifically addresses the picking and allocation of resources, making it more targeted and effective in certain scenarios.
Future of Pick on Pull
As technology continues to evolve, the future of pick on pull looks promising. Advances in artificial intelligence, machine learning, and IoT will further enhance its capabilities, enabling businesses to achieve even greater levels of efficiency and responsiveness.
According to a report by McKinsey, companies that embrace digital transformation in their operations are more likely to succeed in the long term. This highlights the importance of adopting innovative methodologies like pick on pull to stay competitive in today's market.
Conclusion
Pick on pull represents a powerful methodology for optimizing processes and driving efficiency. By aligning supply with demand, businesses can reduce waste, improve productivity, and enhance customer satisfaction. This guide has provided a comprehensive overview of pick on pull, covering its history, benefits, implementation, and future prospects.
We encourage you to explore the possibilities of pick on pull in your operations and share your experiences with us. Leave a comment below or check out our other articles for more insights into productivity and efficiency.
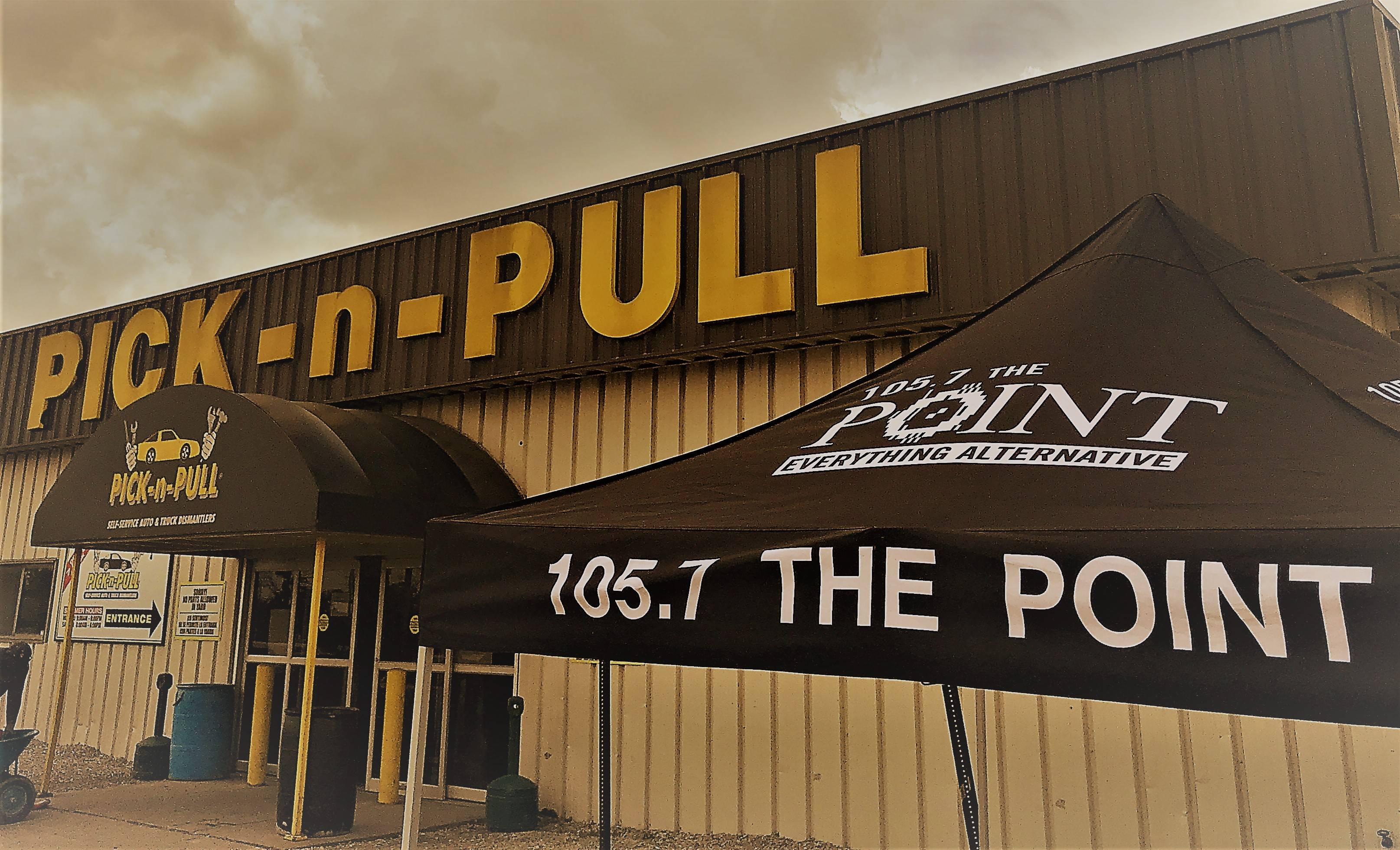
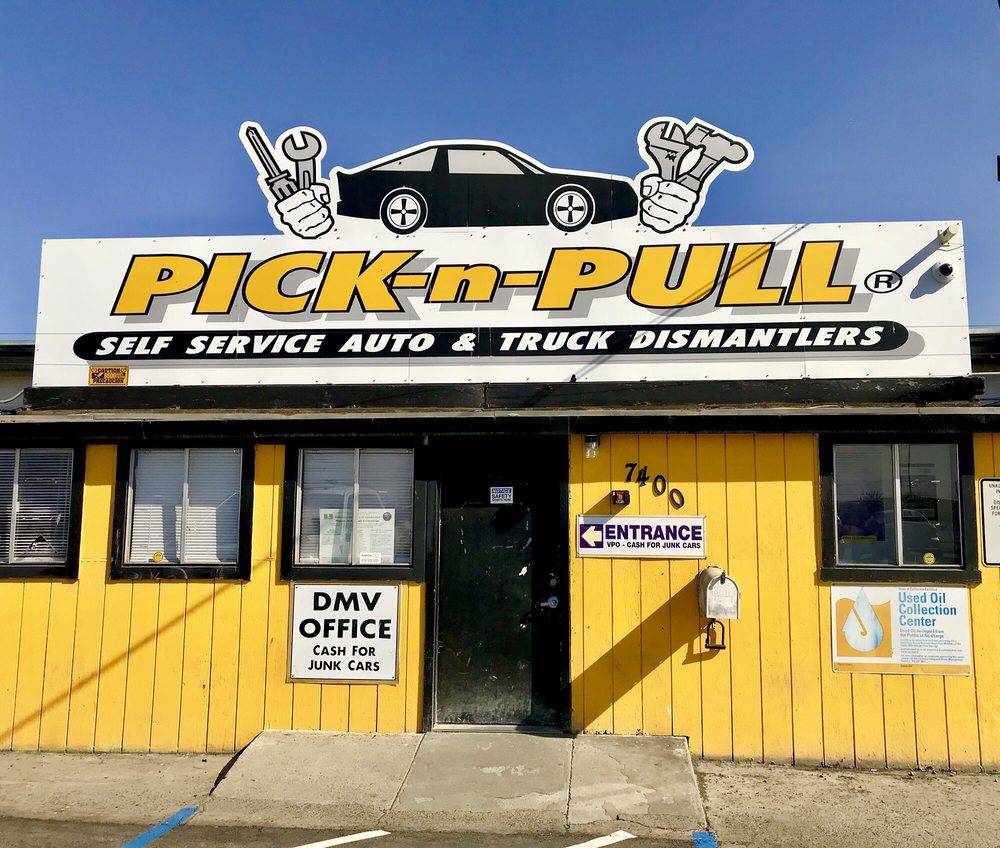